Uptime is the only time that matters!
Yogurt
You Should Expect Our Yogurt Culture to Blend With Yours.
These days every dairy category is rife with competing
and demands. So we deliberately synchronize our technology to leverage your brainpower. Of all the dairy segments – the yogurt category may well be the most demanding, changeable and complex. Multiple flavor options, product formats, PET, glass, wide-mouth, pouch, single chamber and twin chamber cups and other package geometries, health benefits, retailer display requirements, post-consumer environmental issues all impact your secondary and tertiary yogurt packaging strategy.We’ll Keep Your Filler Running So You Can Focus on Research, Variety, Flavor, Customers and Profitability.
Frequent changeovers can seem like a constant drain on productivity. We know that ultimately, uptime on your packaging line is the only time that matters. The project feasibility, system engineering and line integration team at IPM has a yogurt culture. We know your time is split between yogurt varieties, consumer packaging preferences, retailer expectations, multiple setpoints, automation, food safety, changeover complexity and personnel training and retention. This positions us as a leading yogurt packaging integrator.
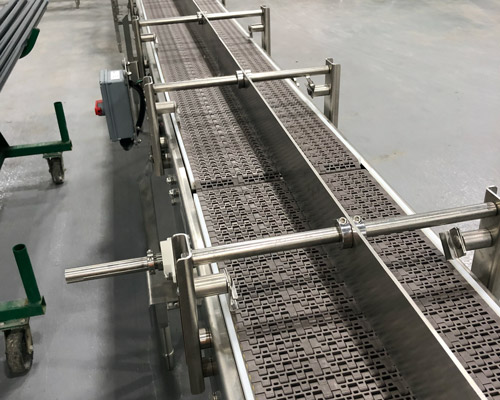
When It Comes To Integration
We don’t manufacture all the machine center technology on a line. But we do know who makes the best for any given packaging line scope. So, even on a new line we will specify OEM equipment that we don’t make but that is ideally suited to your operation. This SURE-thing approach gives you access to our integration experts who are gurus at achieving targeted line runnability by getting the most out of the OEM equipment you prefer or we specify.
We’ll organize and manage all of the vendors and subcontractors in a design-build project delivery mode. This approach establishes a single responsible source, reduces timelines, and reduces FAT complexity, schedule and money. An additional benefit of the IPM SURE-thing sole source integration solution is that the lines’ footprint is typically smaller, and, the line, per agreed scope can be future-proofed for maximum forward looking flexibility.
When It Comes To Accumulation
Properly staging and spacing primary packaging we’ll help you improve line efficiency and reduce product jam ups, spillage and product damage. We’ll help you manage proper line pressure and protect the integrity of the yogurt, and the primary package aesthetics — whether you’re waiting for the process or the filler.
So, although tapered tubs, flexible pouches, PET bottles, single or twin-chamber cups all behave differently coming out of the filler we will work with you to deliver optimal uptime throughout the downstream.
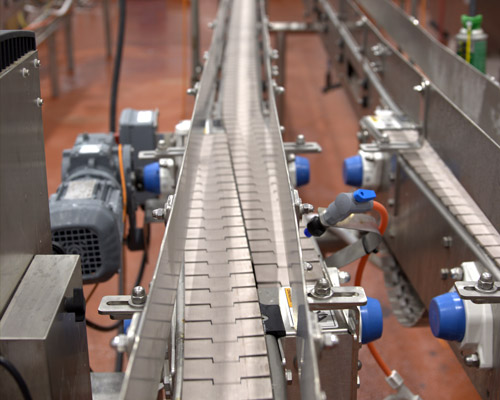
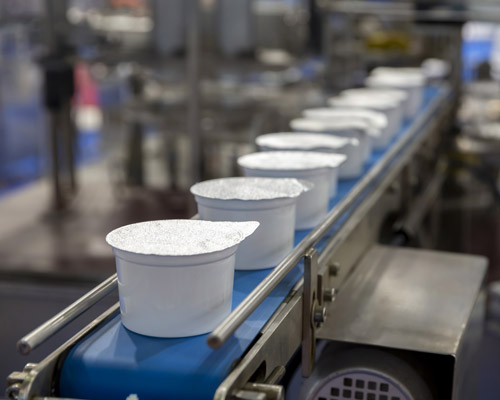
When It Comes To Conveying
We’ll provide precise product placement into and between the checkweighing, labeling, date coding, casing, cartoning, and palletizing machine centers at optimal throughput. We’ll minimize system stoppages and achieve near-zero product damage. Conveyor specification and performance is at the heart of secondary and tertiary packaging.
No matter how efficient your fillers, wrappers, casers and cartoners are, if the line doesn’t integrate conveyor technology, features and advantages engineered and tuned specifically for runnability then product temperature and quality, packaging speed, throughput and cost-efficiency of the entire production and packaging line will be compromised.
When It Comes To Automation
Few things are as important as automating conveyor performance used to transport, stage and index products into and out of the various packaging automated systems along the line. Minimizing conveyor line stoppages significantly decreases opportunities for product jam ups and damage.
Engineering the entire packaging function in your plant to maintain a steady state condition increases line efficiency and throughput profitability. Packaging will be moving at variable speeds at various phases of the packaging and conveying system.
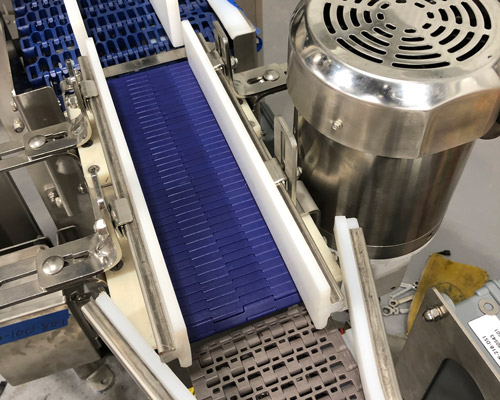
Frequent and rapid changeovers are automated to optimize repeatability, accuracy and uptime!
There are multiple mission-critical functions throughout the secondary and tertiary packaging process. When strategically automated and confidently controlled they can add value, improve safety and debottleneck the post-filler processes. System stops and brakes enable intentional stops and starts to maintain targeted infeed rates and orientation into downstream machine centers. Package lift, transfer and package rotate devices are used to optimize seamless package transition at speed or to change the orientation of products on the conveyor for dating or labeling. Package positioners are used to present the packaging prior to a particular process or to streamline lane changes and merges. Other devices will combine multiple products, in sequence, for multipack configurations.
Uptime Matters!
Packaging systems uptime is mission critical. After you’ve invested all that capital in consumer and retailer feedback, raw materials selection, technology, laboratory research, experienced people, resident brainpower and the primary branded package — who will you trust to case, carton, convey and palletize the ice cream safely from filler to cold storage?
Our facility planning and feasibility team will assess your current packaging technology, physical plant and growth aspirations and work with you to establish performance goals that end with an agreed scope freeze focused on uptime performance.
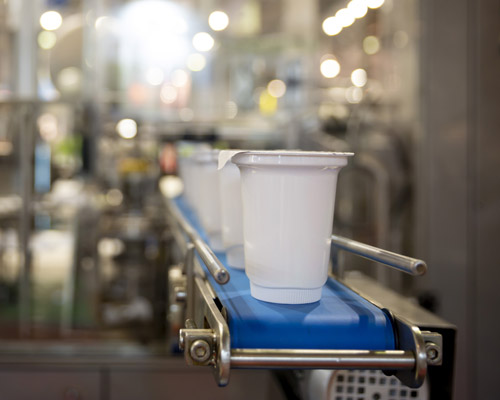
This SURE-thing approach equips us to provide you the best integrated packaging system, or, packaging machine center solution best suited to your plant, your product and your commercials aspirations; including:
- Purpose-specific and future-looking features, benefits, advantages.
- Functionality and control oriented to your product and production goals and configured to package, or reject, primary packaging that falls outside of targeted retail parameters.
- Conveyance, pick-and-place and automation options designed around primary product size, speed and secondary packaging needs.
- Best-fit food grade technology from a variety of best-suited OEM’s with no risk bacterial harborage, and calculated to reduce washdown time and water consumption.
- Depending on your current need, product strategy, retail requirements and production aspirations we can build in an expandable level of automation and the most efficient control, expansion capability, schedule and budget.