How Do Cobot Palletizers Streamline Operations?
The packaging industry is evolving rapidly, driven by the need for efficiency, precision, and cost-effectiveness. One of the most significant advancements in automation is the introduction of collaborative robots, or cobots, in palletizing operations. Unlike traditional industrial robots, cobot palletizers are designed to work alongside human operators, improving productivity while reducing operational costs. By integrating cobots into palletizing tasks, manufacturers can streamline their processes, cut labor expenses, and enhance overall efficiency.
The Challenges of Traditional Palletizing
Palletizing is a critical yet labor-intensive process in packaging facilities. Traditionally, this task has been performed either manually or with large, fixed industrial robots. Manual palletizing presents several challenges, including:
- High Labor Costs: Hiring and maintaining a workforce for repetitive palletizing tasks can be expensive, especially with rising wages and labor shortages.
- Workplace Injuries: Repetitive lifting and stacking can lead to musculoskeletal injuries, increasing workers’ compensation claims and absenteeism.
- Inconsistent Performance: Fatigue and human error can result in improperly stacked pallets, leading to inefficiencies and potential damage during transportation.
- Limited Scalability: As production demands increase, manufacturers may struggle to scale operations efficiently with a manual workforce.
Industrial robots have traditionally been used to address these challenges but come with their own drawbacks, such as high initial costs, complex programming, and large spatial requirements. This is where cobot palletizers provide a game-changing alternative.
How Cobot Palletizers Streamline Operations
Cobot palletizers offer an efficient, cost-effective solution for modern packaging lines. Their flexibility, ease of deployment, and ability to work safely alongside humans make them a valuable asset in manufacturing. Here’s how they help optimize palletizing operations:
1. Reducing Labor Dependency and Costs
One of the primary advantages of cobot palletizers is their ability to perform repetitive palletizing tasks with minimal human intervention. By automating these functions, businesses can significantly reduce reliance on manual labor, thereby lowering operational costs. Cobots do not require salaries, benefits, or breaks, making them a cost-effective alternative to traditional labor.
Additionally, cobots mitigate the risks associated with labor shortages, which have become a growing concern in the
sector. With fewer workers required for palletizing tasks, businesses can reallocate their workforce to more value-added roles, such as quality control or machine maintenance.“Manufacturers looking to stay competitive should consider integrating cobot palletizers into their operations to capitalize on the benefits of reduced labor costs, improved safety, and increased productivity. “
2. Enhancing Productivity and Output
Unlike human workers, cobots can operate continuously without fatigue, resulting in higher throughput and efficiency. Traditional manual palletizing may be subject to slowdowns due to worker fatigue, shift changes, or errors. In contrast, cobots maintain consistent performance, ensuring steady production output.
Cobots also operate with high precision, minimizing errors in stacking patterns and reducing the risk of pallet instability during shipping. This level of accuracy enhances overall operational efficiency, ensuring that products reach their destination safely and in optimal condition.
3. Improving Workplace Safety
Workplace injuries due to heavy lifting and repetitive movements are a significant concern in palletizing operations. Cobot palletizers help mitigate these risks by taking over physically demanding tasks, reducing the likelihood of strain-related injuries.
Moreover, cobots are designed with built-in safety features, such as force-limiting sensors and collision detection, allowing them to work safely alongside human operators without the need for extensive safety barriers. This makes them an ideal solution for facilities looking to improve ergonomics and safety standards.
4. Easy Integration and Scalability
Unlike traditional industrial robots, which often require extensive reprogramming and setup, cobot palletizers are designed for easy deployment and adaptability. Many cobots feature user-friendly interfaces that allow operators to program new palletizing patterns with minimal training. This flexibility enables manufacturers to adjust their palletizing operations quickly in response to changes in product lines or packaging requirements.
Additionally, cobots can be integrated seamlessly into existing production lines without requiring significant modifications to facility layouts. Their compact footprint makes them an excellent choice for businesses with limited space, allowing for more efficient use of available resources.
5. Lower Total Cost of Ownership
While the initial investment in cobot palletizers may seem significant, their long-term cost savings make them a financially sound investment. Unlike traditional industrial robots, cobots have lower installation and maintenance costs. They require minimal upkeep and have a longer lifespan, reducing the overall cost of ownership.
Furthermore, cobots consume less energy than larger automated systems, leading to reduced operational expenses over time. Their ability to work efficiently without the need for excessive power makes them an environmentally friendly and cost-effective solution for modern packaging lines.
Real-World Applications of Cobot Palletizers in Packaging
Several industries have already adopted cobot palletizers to optimize their packaging processes. In the food and beverage sector, for example, cobots handle the repetitive task of stacking packaged goods onto pallets with precision and speed. This not only improves efficiency but also ensures compliance with hygiene and safety regulations by minimizing human contact with products.
Similarly, in the dairy industry, cobot palletizers streamline operations by efficiently stacking cartons, bottles, or pouches, reducing the time required to prepare products for distribution. Their ability to handle various packaging formats makes them a versatile solution for manufacturers with diverse product lines.
The Future of Cobot Palletizing
As automation continues to advance, cobot palletizers will play an increasingly important role in the packaging industry. Ongoing innovations in artificial intelligence and machine learning will further enhance their capabilities, enabling even greater levels of efficiency and adaptability.
Manufacturers looking to stay competitive should consider integrating cobot palletizers into their operations to capitalize on the benefits of reduced labor costs, improved safety, and increased productivity. With their ability to streamline palletizing tasks and support dynamic production needs, cobots represent the future of packaging automation.
Packaging Integration Solutions from IPM
Cobot palletizers offer a powerful solution for packaging manufacturers seeking to optimize their operations. By reducing labor costs, increasing output, and improving workplace safety, these advanced robotic systems are transforming palletizing into a more efficient and cost-effective process. As technology continues to evolve, businesses that embrace cobot palletizers will be better positioned to thrive in an increasingly automated and competitive market.
Contact us at (616) 531-7758 or message us here to find out what we mean when we say, “Uptime is the only time that matters!”
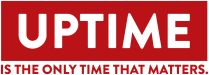