Uptime is the only time that matters!
What is SURE-thing Performance?
A SURE-thing = Specified for Uptime + Runnability Engineered.
One machine center that goes down or slows down impacts the efficiency of your entire packaging line. It’s clear then that uptime performance of a single machine is not the real issue. The real issue is uptime across the entire line. IPM’s SURE-thing performance & uptime scope is centered on integrating all of the technology and all of the performance throughout the secondary and tertiary packaging downstream of the filler to meet your production goals.
Every integrated packaging solution we recommend, install, and commission is Specified for Uptime. But that’s just the first step. The second, and real-world step, is to ensure that the specified technology solutions are Runnability Engineered. We’ll do that on a new line, a packaging line , or a process island within a packaging line. Keep reading to understand SURE-thing Performance™.
Our SURE-thing™ Process: The fundamentals of an IPM vertical start-up
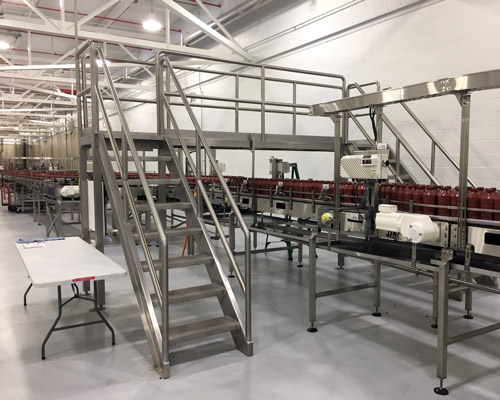
Step 1
Initial Consultation to document Current State and Project Aspirations
- Collect first draft information regarding packaging system goals and aspirations
- A review of the existing process
- Visual assessment of production floor, existing technology, controls and utilities
- Measurements of space
- Review availability and status of utilities and infrastructure
- Document the Current State
- Outline a very high-level trio of possible solutions
Step 2
SURE-thing™ (Specified for Uptime. Runnability Engineered.) Scope Freeze
Establishing Scope Freeze is an essential prerequisite to recommending the optimal food packaging line solution. In fact, it’s an imperative when we work together to design and engineer a metrics-driven food packaging system. Your product portfolio might require speed at volume. Or it might require switchover agility. Your commercial aspirations may require less handwork and more automation. Your package type, size, shape, temperature exiting the filler, etc. might require unique control and delicate handling. And your tertiary packaging, storage and shipping protocols might require an especially demanding carton and palletizing solution.
It’s all doable. And we’ve done it all before. But there are always project priorities and must-haves. Each of those are often accompanied with wish-lists and tradeoffs that must be evaluated. The SURE™ thing step in the IPM Method is a low-cost, high-value method that rationally filters out misdirection, promotes collaboration through mutual focus and increases your confidence in a best-fit food packaging solution including:
- Line Audit and Assessment
- Document production goals
- Document physical space
- Document existing machinery
- Collect and prioritize pros, cons and risks input from plant management, plant engineering and operating personnel
- Discuss first draft budget and schedule
- The result is a Project Managed, Milestone-driven set of Project-specific next steps
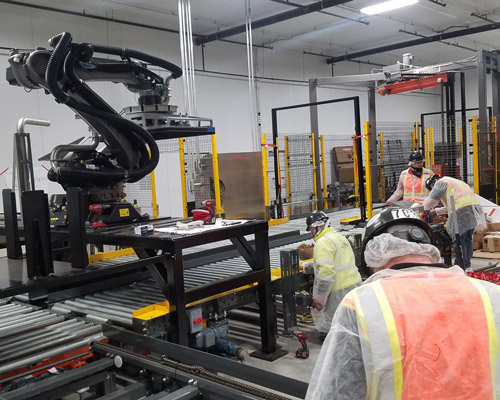
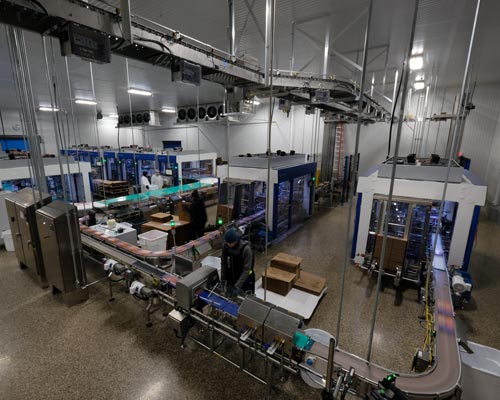
Step 3
Design, Application and Controls Engineering
- Document installation sequence site access, plant traffic, food safety, access to utilities
- Organize all aspects of design, manufacturing and installation for a vertical start-up
- Design line layout speed, accumulation, changeover, food safety, temperature, etc.
- Design automation and control
- Specify third-party technology
- Outline commissioning, start-up, training, and post start-up support plan
Step 4
Fabrication and Assembly
- Ensure that all third-party technology meets specified standards
- Integrate and test all packaging sequences
- Assembled to meet all prevailing Food Safety protocols
- Factory Visits at your convenience
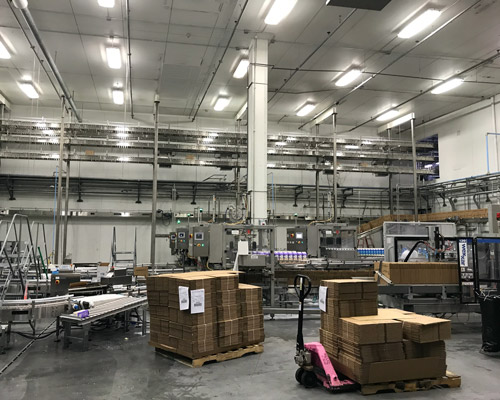
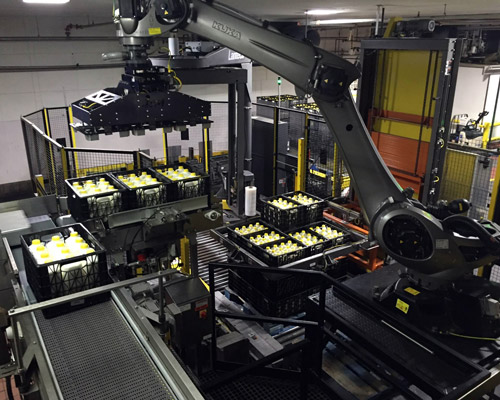
Step 5
Project Management, System Installation & System Integration
- Pre-project organization of all technology, contractors, and plant readiness issues
- Confirm site access, plant traffic, food safety, access to utilities
- Install equipment and controls per plant schedule
- Test installation and control runnability under all targeted operating conditions
Step 6
EQUIPS Training
- Overview of equipment and control including food safety and personnel safety
- Thorough review of all machine operating manuals
- Documentation of HMI
- Basic troubleshooting
- Preventative maintenance

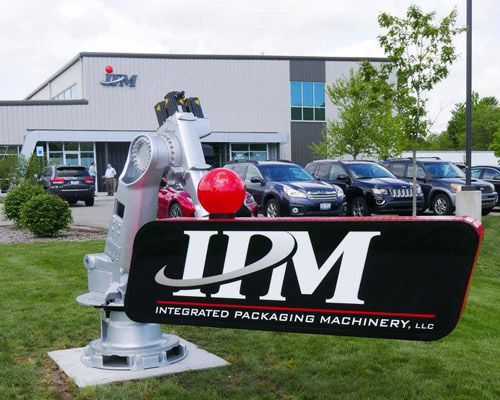
Step 7
Documentation, Spares, Parts & Maintenance, Service & Support
- Documentation of all equipment including drawings, control
- Scheduled runnability, re-training and follow-up services
- Technical support and Customer Service
UPTIME IS THE ONLY TIME THAT MATTERS!
SURE-thing™ packaging solutions backed by those who engineered them
Consistent and debottlenecked performance in a complex highly regulated environment like a food plant is demanding at best. IPM will bring to bear it’s SURE-thing™ approach to ensure you get an intentionally optimized downstream packaging solution that meets your production goals.
Some of the equipment, technology and automation approaches we’ll install is the equipment we design and manufacture. Our technology portfolio and resident thought leadership grew around specifying a food safe packaging solution that we couldn’t find in the market.
But not all solutions work equally well in every instance of speed, food type, package size and shape, production goals, existing capital you already have installed, legacy OEM relationships you intend to maintain combined with issues of temperature, accumulation and dwell times. And so we’ll regularly recommend, specify and buy purpose-specific equipment to meet the production goals and technology preferences of our customers and the Uptime SURE-thing™ assurances of our commitment to you without regard to our product line.
Uptime in the downstream
IPM’s SURE-thing approach could be the right approach for your food or beverage packaging plant or project. Your product portfolio might require speed at volume. Or it might require switchover agility. Your commercial aspirations may require less handwork and more automation.
Your package type, size, shape, and temperature requirements might require strategic accumulation, unique control and delicate handling. And your tertiary packaging, storage and shipping protocols might require an especially demanding carton and palletizing solution.