Supporting Your Workforce in Automation
As automation becomes an essential part of the packaging industry, companies must not only invest in technology but also support their workforce in adapting to these advancements. Industry research on sustainability commitments in U.S. dairy processing found that 89% of respondents ranked streamlining and improving operations as a top priority. The second highest priority? A highly skilled workforce.
As businesses integrate automation solutions into their operations, they must also rethink their approach to hiring, training, and workforce development. However, research from Harvard Business Review highlights a significant challenge: 70% of employees report not having mastery of the skills required for their job, and only 12% apply newly learned skills from training programs in their daily work.
For automation to be successful, companies must bridge this gap with targeted training programs that equip employees with the skills necessary to operate, maintain, and optimize automated systems.
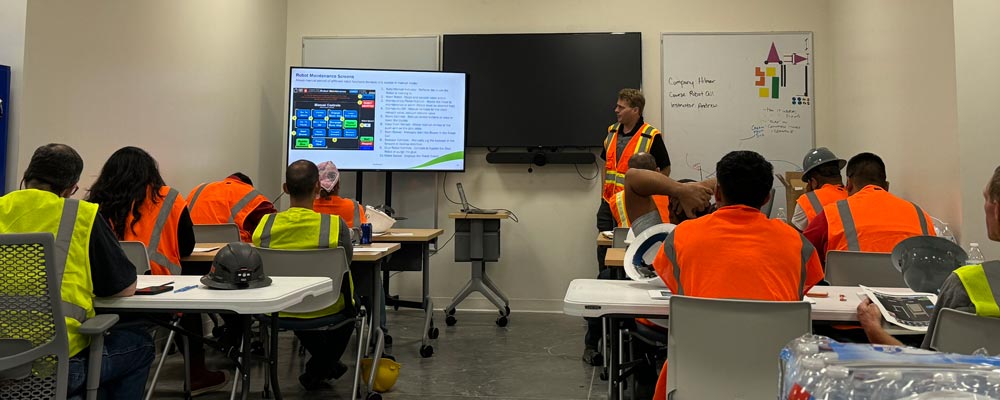
Key Skills for a Workforce in Automation
To effectively integrate automation into packaging operations, companies must focus on training employees in:
- Understanding automation concepts and how they impact workflows
- Utilizing automation tools to enhance efficiency and reduce errors
- Designing and implementing automated workflows to improve productivity
- Troubleshooting automation issues to minimize downtime
- Keeping up with emerging automation technologies to stay competitive
IPM EQUIPS: Training Tailored to Your Needs
At Integrated Packaging Machinery (IPM), we recognize that successful automation is about more than just installing new technology—it’s about ensuring your workforce is prepared to operate and maintain it. That’s why we offer IPM EQUIPS, a demand-based training program designed to meet the specific needs of each customer.
Unlike generic training programs, IPM EQUIPS provides:
- Customized training tailored to your unique automation systems
- A blend of classroom and hands-on learning for real-world application
- OEM-neutral training that ensures employees can confidently operate equipment from multiple vendors
- A dedicated Training Project Manager to coordinate communication, scheduling, and instruction with OEM Subject Matter Experts
Our train-the-trainer approach ensures that your team not only learns how to use automation tools effectively but also gains the knowledge to train future employees, creating long-term sustainability for your operations.
“IPM EQUIPS has helped packaging manufacturers across the U.S. increase uptime, improve operational efficiency, and boost employee confidence in automation.”
Proven Training. Proven Results.
IPM EQUIPS has helped packaging manufacturers across the U.S. increase uptime, improve operational efficiency, and boost employee confidence in automation. With a 94%+ satisfaction rating, our training has been praised by operators and maintenance staff alike:
“Instructors provided in-depth knowledge of all machinery.”
“I’ve been here for 42 years—this was the best training I’ve ever received.”
“Training was maintenance-specific and extremely useful.”
“If the instructors didn’t know an answer, they found it.”
Our goal is simple: Empower your workforce to operate automation safely, efficiently, and confidently.
Why Choose IPM for Automation Training?
IPM doesn’t just install automation solutions — we ensure your team has the tools and knowledge to maximize their potential with these systems. Our OEM-neutral approach means we can train employees on any integrated system, regardless of the
.Whether you’re looking to improve operations, reduce downtime, or establish a consistent training program, IPM EQUIPS is your SUREthing solution for workforce development in automation.
Ready to train your team for the future of packaging automation? Contact IPM today to learn more about how IPM EQUIPS can transform your workforce.
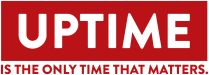