Uptime is the only time that matters!
ESL Product
Aseptic Packaging for Food & Beverage Processors
You’ve invested a boatload of money and brainpower in aseptic processing technology to produce a competitive ESL product. The processing, cooling, unit filling and capping sequence is obviously a mission-critical one. Before that you invested earlier dollars and proprietary know-how in engineering a competitive primary packaging and capping solution to complement your distribution strategy. And after that, even more dollars to ensure your shelf-ready package design accurately reflects your brand – a brand and level of performance that meets wholesaler requirements, and, cosumer expectations.
Who will you trust to protect your ESL product in the downstream?
IPM has been engineering post-filler secondary and tertiary packaging solutions for ESL product in aseptic primary packaging for a very long time. We have helped both international and regional food and beverage processors ensure the integrity of their aseptic package as well as their ESL business model.
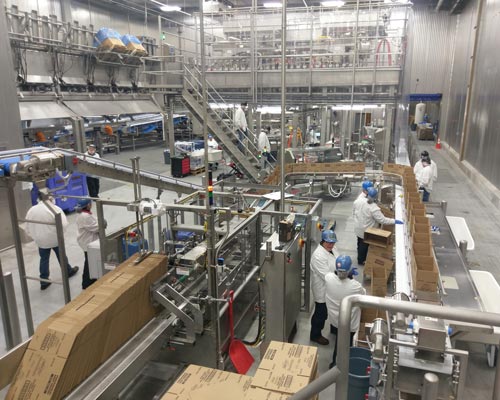
IPM has engineered post-filler integrated packaging systems at every scale. Regardless of primary package materials of construction, size, shape, weight, temperature, or variety of SKU’s exiting your ESL filler. Through it all, the IPM value proposition, “Uptime is the only time that matters!” is evident in every machine center, every control solution, and runs through every F.A.T., every training workshop, and in every customer support and service interaction.
The IPM SURE-thing approach is a proven combination of experience, thought-leadership and accumulated hands-on commitment to protecting your aseptic primary package investment throughout the downstream integrated packaging system at your scale and per your schedule.
When it comes to post-filler aseptic package handling, experience trumps good intentions.
Packaging of pre-sterilized and sterile products like milk, puddings, desserts, fruits, juices and vegetables, and packaging of non-sterile products such as fermented dairy products are costly to make and package. Some aseptic primary packaging formats are more common than others. We’ve been presented with all of them. And all of them require intentional line efficiency and line uptime strategies before they can contribute to product line profitability.
ESL products in aseptic cartons
Stand up gable top of box cartons composed of layers of unbleached or bleached paperboard coated internally and externally with polyethylene designed to be impermeable to liquids combined with a thin layer of aluminum providing an oxygen and light barrier.
They require uniform handling to optimize the speed and accuracy of the case-packing functions and careful control throughout the secondary and tertiary packaging system to maintain the integrity of the seal, the laminar carton construction – and to maintain the targeted uptime. Trust IPM as your source for aseptic packaging of milk and other ESL products.
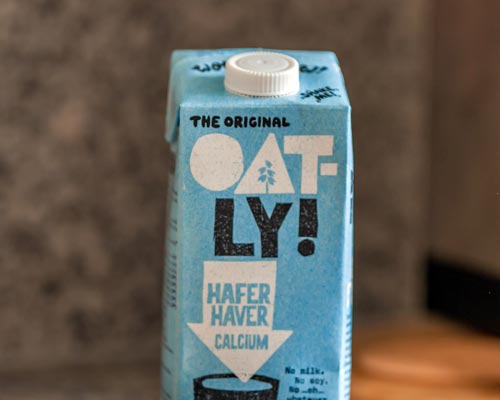
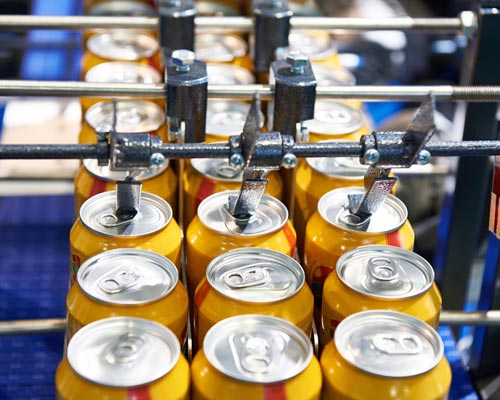
ESL product in aseptic cans
Sterilized cans filled with sterile product and sealed to maintain a vacuum in the cans. Typically require a serious accumulation function before being presented, at speed, to downstream functions.
Their uniform shape requires a careful orientation solution through the inspection function to ensure proper label position presented to the inline date encoder, and to detect leakers. They require careful handling to optimize the speed and accuracy of the case-packing functions and careful control throughout the secondary packaging system to maintain the integrity of the label and the targeted uptime.
ESL product in aseptic bottles
Typically, plastic bottles, and sometimes glass bottles. HDPE and PP are the two most common thermoplastics with pigments added to protect the contents from light. Typically used for packaging a variety of products ranging from non-dairy creamers to plant-based and dairy milk and fruit juices.
Depending on bottle shape they typically require proper orientation through the inspection function to ensure proper label or sleeve wrap position and to detect leakers. Plastic bottles require careful handling to prevent punctures and optimize the speed, accuracy, and uptime of the case-packing functions.
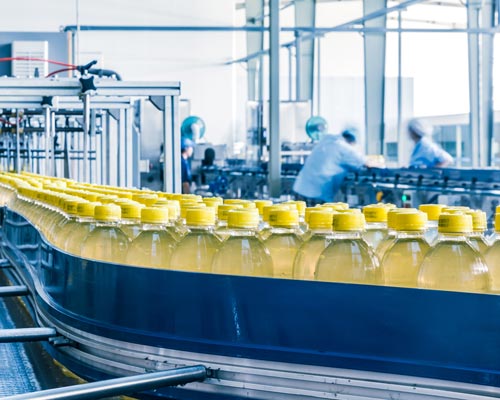
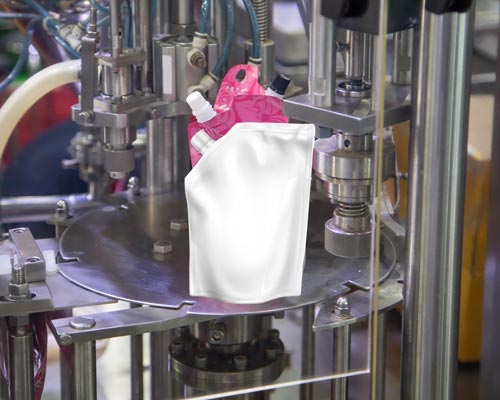
ESL product in aseptic pouches
Pouches are typically part of our customers’ environmental strategy to improve energy consumption and reduce waste. We’re seeing more and more pouches of all shapes and sizes, including bag-in-box formats. The pouches are typically made of an opaque film to exclude light and odor.
Pouches are sometimes difficult to handle because of their pliable construction, their unpredictable pattern exiting the filler, and because they are prone to punctures. Proper accumulation sometimes plays a role in improving throughput.
ESL product in aseptic cups and tubs
Often made of paper with wax or plastic coating on the inside. Used for frozen and coagulated products. Sometimes a demanding secondary packaging application because of their small size or trapezoidal bowl shape, their top foil seal configuration and in some cases their snap-apart design and “side car” format.
They require careful handling downstream to prevent foil top seal punctures, edge, or bowl crush and to optimize uptime throughout the secondary and tertiary packaging functions.
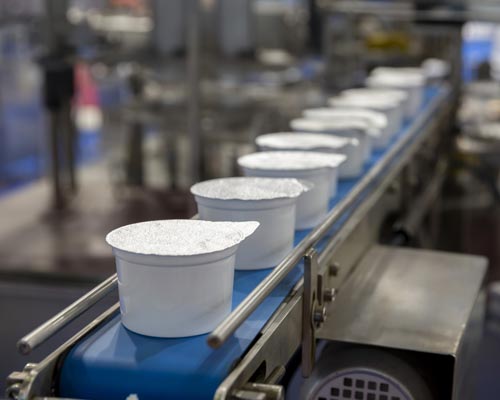